How to achieve zero leakage of soft seal gate valve DIN3352
Release Time:
Jul 24,2025
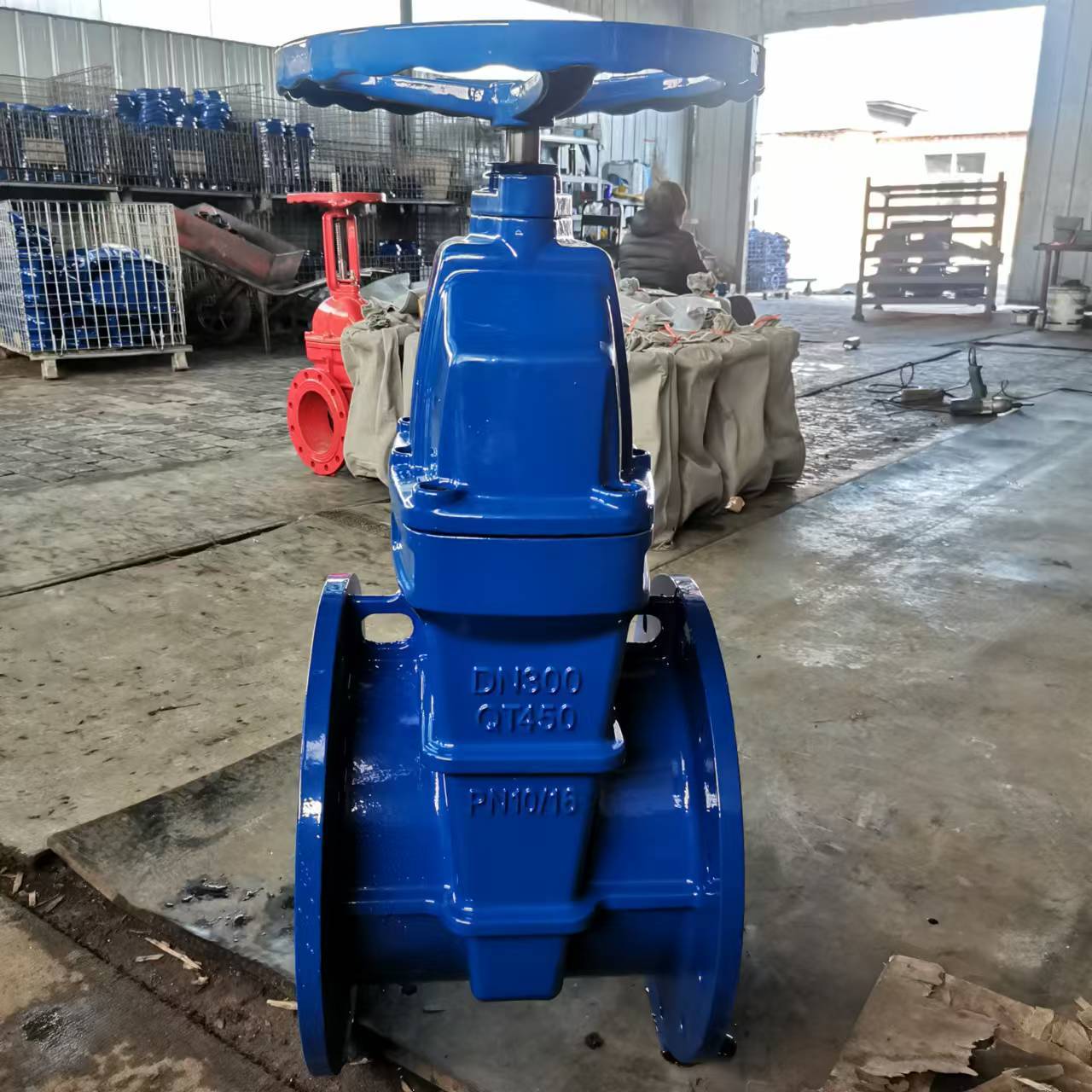
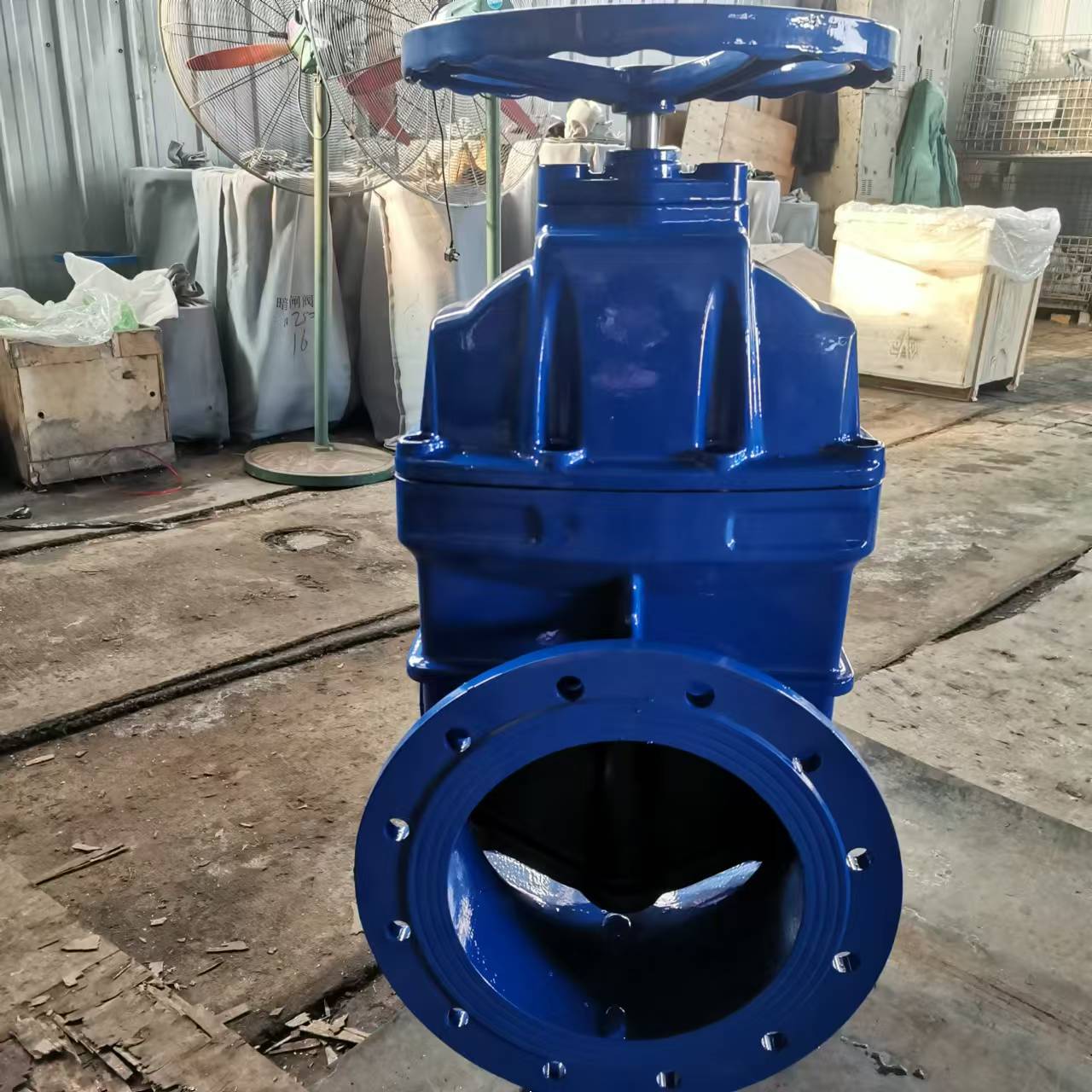
How to achieve zero leakage of soft seal gate valve DIN3352? The key to this type of valve lies in the elastic sealing ring, usually made of rubber or polymer material, which contacts the valve seat to achieve sealing. DIN3352 is a German industrial standard that specifies dimensions and materials, so design and manufacturing must comply with this standard.
Next is the design of the sealing structure. When the valve is closed, the valve plate presses the sealing ring tightly, and this compression amount is very important. Too big can accelerate aging, too small may leak. In addition, the roughness of the valve seat surface should be well controlled. If it is too rough, it will wear out the sealing ring, and if it is too smooth, it may not be conducive to fitting. Is it possible to design the valve seat with a slight slope? This way, when closing the valve, it can gradually tighten and avoid impact.
Manufacturing accuracy cannot be ignored either. If the coaxiality of the valve plate and valve seat is not accurate, the sealing will be uneven. When processing, CNC machine tools must be used to ensure dimensional tolerances, especially the accuracy of the sealing surface. The assembly process is equally crucial, and the sealing ring must be installed in place without distortion or damage. The sequence and force of bolt tightening should be uniform, otherwise the valve body may deform.
The following are the key elements to achieve zero leakage:
High quality sealing materials and optimized design:
Sealing ring material: This is the most critical factor. High quality, medium resistant, temperature resistant, aging resistant, and low compression set elastic materials (such as EPDM, NBR, FKM, etc.) must be selected. The material formula needs to be optimized for specific application conditions (medium, temperature, pressure).
Sealing ring structure design:
Geometry: Optimize the cross-sectional shape of the sealing ring (such as lip shape, O-ring with retaining ring, specific contour) to ensure effective fit with the valve seat under both low and high pressure, providing initial sealing and pressure assisted sealing.
Compression: Accurately calculate and control the compression of the sealing ring when the valve is closed. Excessive compression can lead to premature aging and failure, while insufficient compression cannot guarantee sealing. The design should ensure that sufficient sealing pressure can be maintained throughout the entire working life cycle.
Support and protection: Consider adding metal or high-strength plastic support rings inside or on the back of the sealing ring to prevent excessive deformation (extrusion) or collapse of the sealing ring under high pressure or frequent opening and closing.
Valve seat design:
Surface smoothness: The sealing surface of the valve seat in contact with the sealing ring must have a very high smoothness (low roughness Ra value) to avoid scratching the sealing ring or forming leakage channels.
Flatness and angle: Ensure extremely high geometric accuracy of the sealing surface (flatness, perpendicularity to the valve stem axis, or design angle).
Material: The valve seat body (usually a part of the valve body) should have sufficient strength and stiffness to avoid deformation under bolt preload or pipeline stress. Sometimes it may be considered to use valve seat inserts with better corrosion resistance.
Precision manufacturing and processing:
Critical dimensional tolerances: Strictly control all critical dimensional tolerances related to sealing on the valve body, valve cover, and gate (valve disc), especially the diameter, flatness, position of the gate guide groove, and stem stroke of the valve seat sealing surface. Compliance with DIN 3352 is the foundation, and pursuing zero leakage may require stricter tolerances.
Surface treatment: The sealing surface of the valve seat needs to be finely ground, ground or polished to achieve a very high smoothness (Ra value is usually required to be 0.4 μ m or lower).
Coaxiality/Verticality: Ensure highly accurate geometric relationships (such as coaxiality and perpendicularity) between the sealing surface of the valve seat, the axis of the valve stem, and the cavity in the valve body. This ensures that the sealing ring can be evenly pressed tightly when the gate is closed.
Rigorous assembly process:
Cleanliness: The assembly environment (clean room or strictly controlled area) and components must be highly cleaned to prevent foreign objects such as dust, particles, oil stains, etc. from contaminating the sealing surface.
Sealing ring installation: The installation of the sealing ring must be standardized to avoid twisting, excessive stretching, or scratching. Use appropriate lubricants (compatible with the medium).
Bolt tightening: The connecting bolts between the valve body and the valve cover must be uniformly tightened according to the specified torque and sequence to ensure reliable sealing of the valve body flange (gasket or O-ring) and prevent deformation of the valve body from affecting the internal valve seat.
Guidance and Alignment: The movement of the gate plate inside the valve body must be smooth and unobstructed, and the precise guidance structure ensures that the gate plate (along with the sealing ring) can perfectly align with the valve seat when closed.
sale@cnbestvalve.com WhatsApp: +8613333075295