Technical Description of Rubber Disc Check Valve
Release Time:
Jul 23,2025
Technical Description of Rubber Disc Check Valve
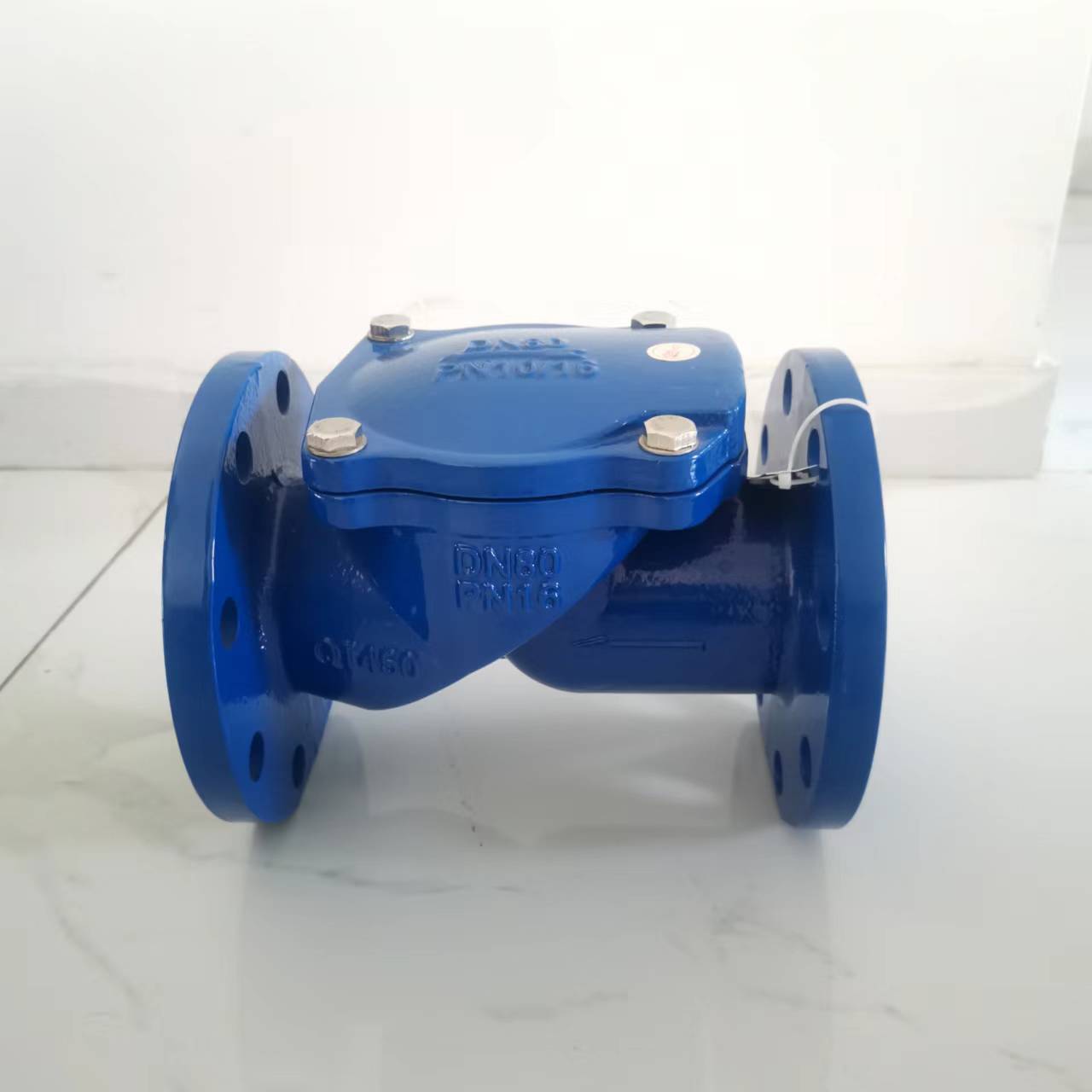
The H44X (SFCV) series rubber flap check valve adopts a full flow area design, which has the characteristics of low head loss, less accumulation of debris, and easy maintenance. The rubber disc in the valve is made of steel plate, steel rod, and reinforced nylon cloth as the substrate, and the outer layer is made of flat plate vulcanization and overall encapsulation technology. The valve disc can have a switching life of up to 1 million times.
Technical description of rubber flap check valve:
① Nominal diameter: DN50-DN600; Nominal pressure: 1.0Mpa, 1.6Mpa
② Adopting a full flow area design, the head loss is small, it is not easy to accumulate debris, and maintenance is simple.
③ The rubber flap is made of steel plate as a pressure bearing component, covered with reinforced nylon cloth, and the outermost layer is made using hot vulcanization integral encapsulation technology. The nylon fibers added to the rubber flap can form an elastic reinforcement between the steel plate and the steel rod, allowing the valve to open and close frequently without breaking.
1. Valve body
④ The closing stroke of the check valve is relatively small, with a stroke angle of only 35 ° to achieve full opening. Under the action of reverse water flow, the closing speed is fast, reducing the occurrence of water hammer and preventing the medium from flowing back into the water system, causing losses to the water system and damage to the pump.
⑤ The check valve body is marked with an arrow indicating the direction of water flow.
2. Component material
① The valve body is made of ductile iron (QT450)
② The valve cover is made of ductile iron (QT450)
③ The valve disc is made of carbon steel, reinforced nylon, and NR rubber
3. ① Valve body. Clean and polish the inner and outer surfaces of valve covers, etc
② The inside and outside of the valve are coated with electrostatic spraying - non-toxic epoxy resin powder coating to prevent rust and fluid corrosion.
③ The coating is smooth, uniform, and defect free. The coating does not dissolve in water and does not affect water quality. It does not change due to changes in air temperature.
④ The coating thickness can reach over 300um, and the powder coating meets the hygiene requirements for drinking water.
4. Valve inspection
Hydrostatic test: Shell strength test: The test strength is 1.5 times the pressure and there shall be no water leakage
Valve seat sealing test: The experimental strength is 1.1 times the pressure and there shall be no water leakage